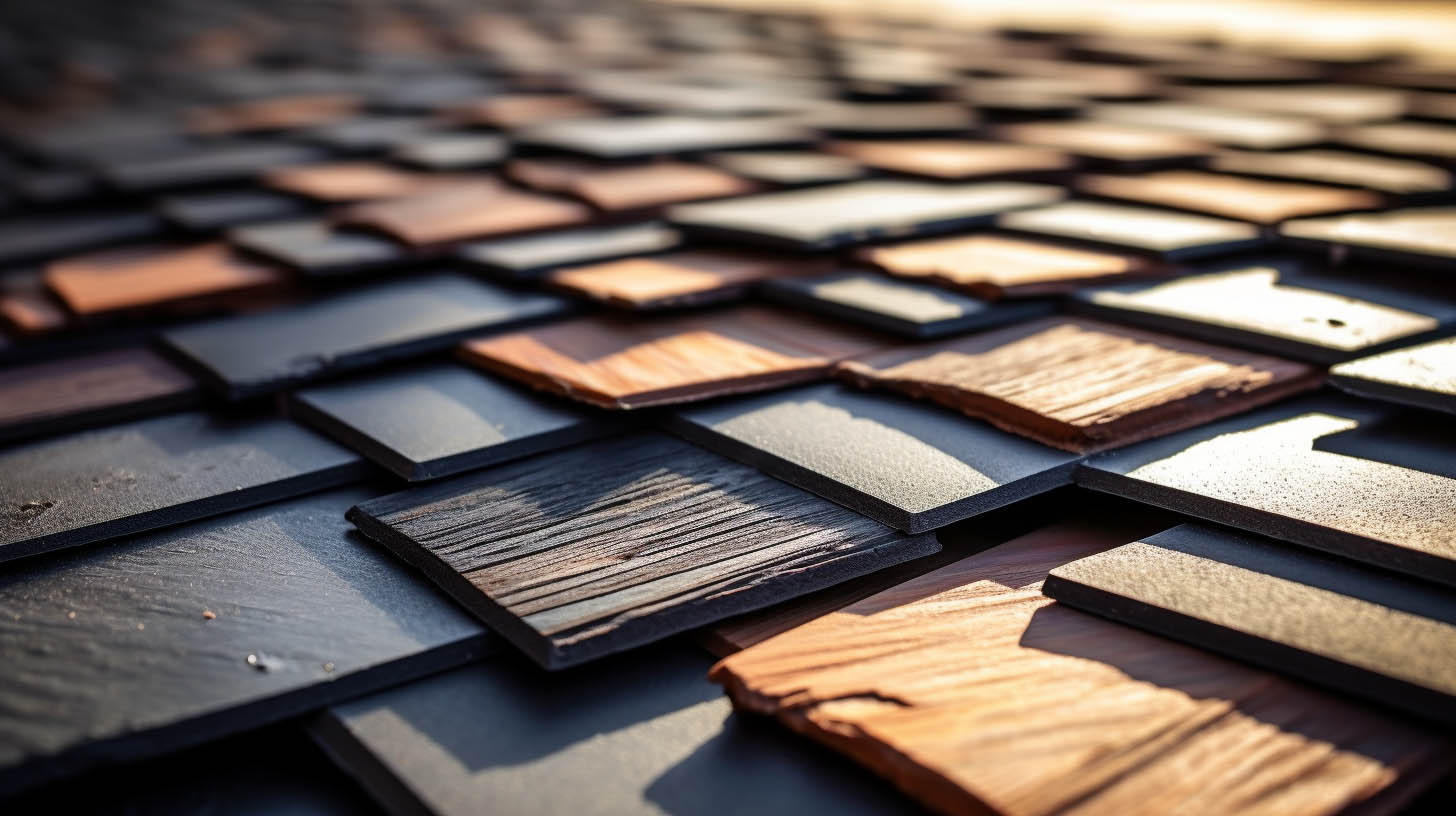
The Guide to Shingle Manufacturing: Unveiling the Process
Shingles, a cornerstone in roofing materials, have a rich history and a complex manufacturing process. Their evolution from simple wooden pieces to modern asphalt-coated variants reflects advancements in technology and materials science. In this detailed exploration, we delve into the intricate journey of shingle production, from raw materials to the finished product, ensuring that structures are not only protected but also aesthetically enhanced.
A Historical Perspective on Shingles
Shingles have been a fundamental roofing material since the colonial 1700s, initially crafted from wood. These early shingles were thin, rectangular wood pieces, installed in overlapping rows – a method still prevalent today. The late 19th century marked a significant evolution with the introduction of asphalt-coated shingles, which quickly became a North American standard. This innovation brought enhanced durability and waterproofing, elevating the shingle’s functional and protective qualities.
Selecting the Right Base Material
The choice of base material is pivotal in shingle manufacturing. Two primary types exist: organic and inorganic. Organic bases, typically made from paper saturated with asphalt, offer certain advantages but are more prone to fire. In contrast, inorganic bases, often comprising fiberglass or synthetic materials, provide enhanced weight and fire resistance, albeit at a higher cost. This crucial decision impacts the shingle’s final properties and suitability for various roofing projects.
The Manufacturing Process: A Step-by-Step Breakdown
Dry Looping: This initial phase involves coating the base material with asphalt, not once but twice, enhancing the shingle’s resistance to water and weather damage. The asphalt quantity dictates the shingle’s final weight.
Saturation: Here, the base material undergoes saturation with hot asphalt, increasing its pliability. This step is crucial for the shingle’s flexibility and durability.
Wet Looping: The base material is then shaped into an accordion-like form, giving shingles their unique three-dimensional appearance. This shape is key to their resistance to wind and wear.
Coating: A fine mineral particle-mixed asphalt is applied to the shingles, providing additional elemental protection. This coating process is critical for the shingle’s longevity.
Mineral Surfacing: Mineral granules are added to the shingle’s surface, imparting color and UV radiation protection. This step also adds weight, further enhancing wind resistance.
Finishing and Cutting: The shingles are accumulated into large rolls, then cut into specific shapes and sizes, ensuring uniformity and proper fit during installation.
Packaging: Finally, the shingles are bundled for easy transport and storage, ready for shipment to contractors and homeowners.
Ensuring Quality in Shingle Manufacturing
Quality control is integral at every manufacturing stage. It begins with scrutinizing the base material for impurities, ensuring even asphalt distribution, and maintaining consistent temperatures during curing. The final inspection before packaging is crucial to identify any defects, guaranteeing that only top-quality shingles reach the customer.
The Dual Role of Shingles: Protection and Aesthetics
Shingles serve a dual purpose: they are essential for protecting structures from the elements and enhancing aesthetic appeal. Their material diversity ensures effective insulation, keeping interiors comfortable across seasons. Additionally, the wide range of colors and styles available allows for customization to elevate a building’s curb appeal.
In conclusion, the journey of shingle manufacturing is a testament to technological advancement and material innovation. For those considering a new roof, understanding this process is crucial. MaxForce Roofing and Siding LLC, based in Columbus, OH, stands ready to guide you through selecting the perfect shingles for your home or business, ensuring both protection and style.